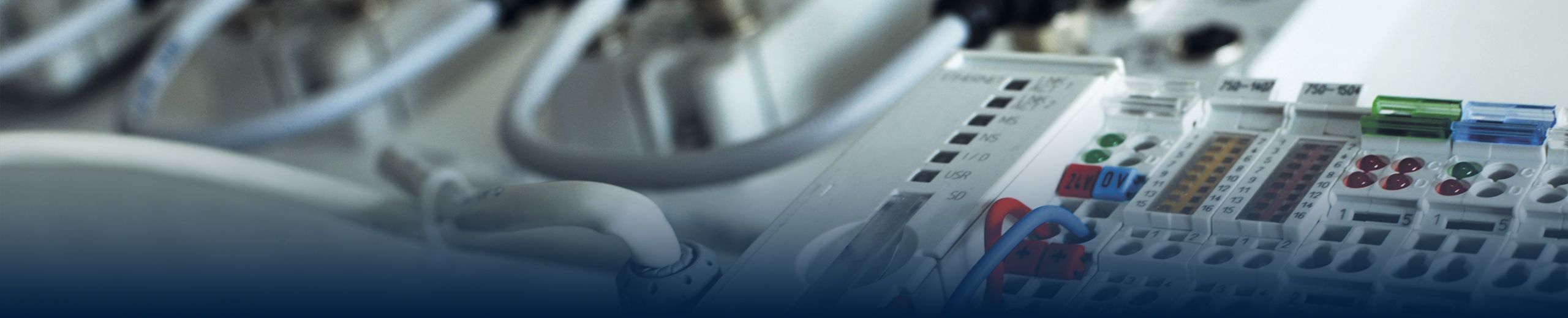
CODESYS Fieldbus & Communication
The wide variety of communication options makes CODESYS a unique automation platform. Whether a connection to classic fieldbuses such as CAN/CANopen®, Industrial Ethernet fieldbuses such as EtherCAT® and PROFINET, general communication protocols such as OPC UA and MQTT or application-specific protocols such as DNP3 and BACnet® - CODESYS offers integrated solutions that you can use immediately.
CODESYS thus enables communication between devices at all levels: Of course, reading and writing inputs and outputs at field level, cross-communication between distributed controllers and other intelligent devices in production lines or mobile machines, but also data exchange between the controller and the control level or the cloud.
CODESYS Fieldbus
The use of I/O data from connected fieldbus systems is a core task of every control platform. CODESYS supports this task with two components:
- Communication libraries that implement the protocol stack
- Adapted configurators for the most important fieldbus and communication systems
The application of the various fieldbus technologies with protocol stack and configurator is almost identical. The graphical configurators allow you to comprehensively manage the fieldbuses and the nodes used. CODESYS also offers you in-depth diagnostic functions such as event loggers or diagnostic information in the device tree. You can even read out the diagnostic information via generic variables in the application and react to it.
Classic fieldbus systems/protocols supported in CODESYS:
- CANopen
- J1939
- PROFIBUS*
- Modbus TCP/RTU
- IO-Link
- KNX®
*is in the service phase
Ethernet-based fieldbus systems/protocols supported in CODESYS:
- EtherCAT
- Ethernet/IP™
- PROFINET
In addition, the CODESYS Development System includes a generic configurator for other bus systems.
CODESYS Communication
In addition to the fieldbuses, communication protocols are available for exchanging data with other systems in the automation environment - for example with other controllers, any other intelligent devices in the network, connected MES or ERP systems or private or public clouds.
You can also access physical interfaces such as Ethernet and serial interfaces from the PLC application and exchange data via important communication protocols such as OPC UA, MQTT or http/https. You can also develop your own protocols directly in CODESYS.
Communication protocols supported in CODESYS :
- OPC UA
- Server/Client
- PubSub
- Building Automation Library
- BACnet
- DNP3
- IIoT library (MQTT, http/https, SMTP/POP3, SNTP, SNMP)
- Basic services for implementing proprietary protocols
- Proprietary CODESYS protocols